The Transformative Power of Injected Molded Plastic in Modern Business
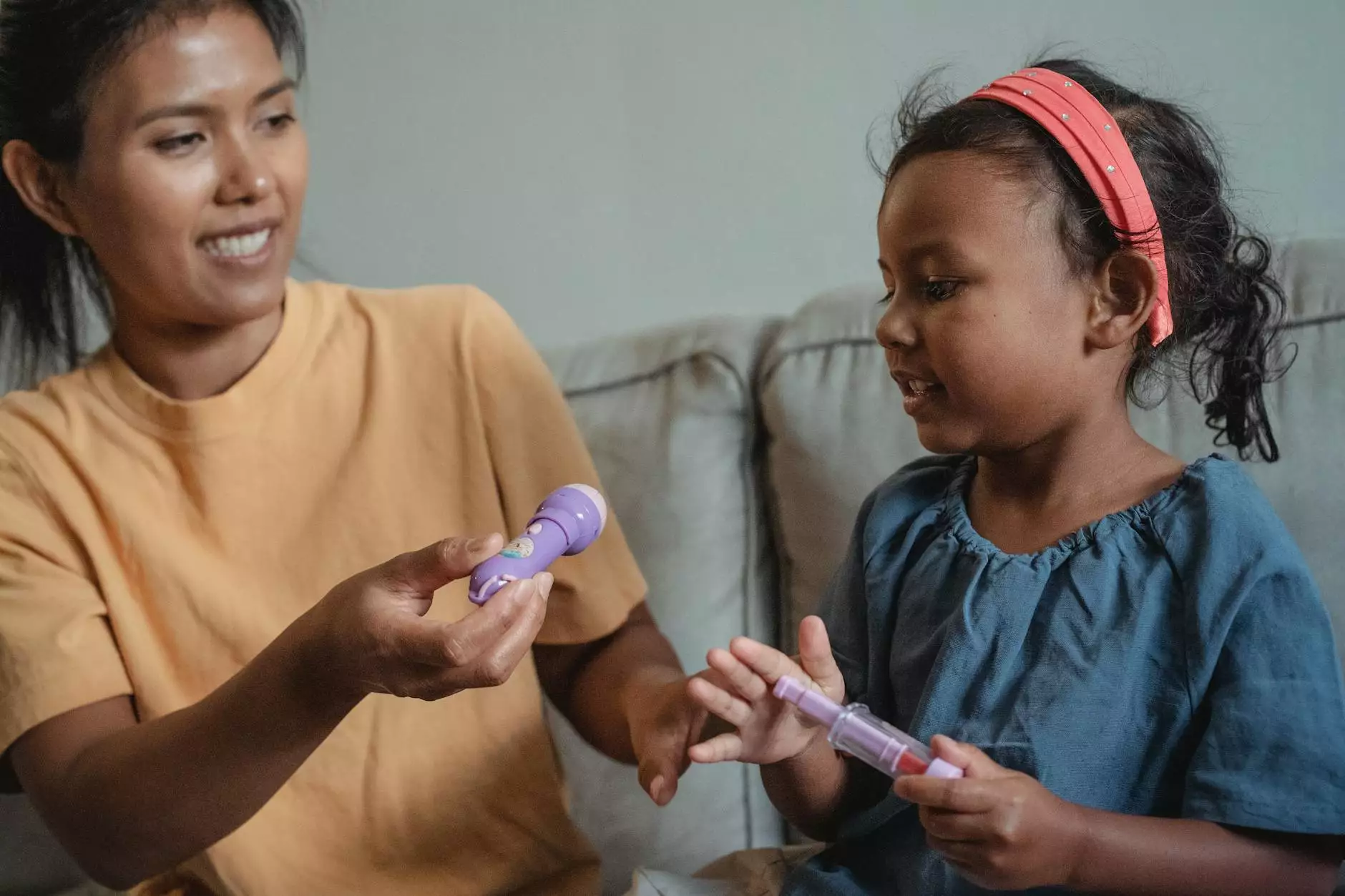
The world of manufacturing is constantly evolving, driven by new technologies and innovative materials. One of the most significant advancements in this realm is injected molded plastic, a process that has revolutionized how products are designed and produced. In this article, we will explore the myriad benefits of injected molded plastic, its applications across various industries, and how companies like deepmould.net are leading the charge in this transformative journey.
Understanding Injected Molded Plastic
Injected molded plastic is a method of manufacturing that involves injecting molten plastic into a mold to create various products. This technique allows for high precision and customization, making it a preferred choice for manufacturers across the globe. Here, we delve into the fundamental aspects of this process:
1. Process Overview
- Material Selection: The process begins with selecting a suitable thermoplastic material. Common choices include polyethylene, polypropylene, and polystyrene.
- Mold Creation: Molds are crafted with high precision, typically from steel or aluminum, to ensure durability and accurate replication of the desired part.
- Injection Process: The chosen plastic is heated until molten and injected into the mold under high pressure.
- Cooling and Ejection: After cooling, the solidified part is ejected from the mold, completing the cycle.
2. Types of Injected Molded Plastics
There are various types of plastics used in the injection molding process. Some of the most commonly utilized include:
- ABS (Acrylonitrile Butadiene Styrene): Known for its toughness and impact resistance, making it ideal for automotive parts.
- PLA (Polylactic Acid): A biodegradable option made from renewable resources, popular in sustainable products.
- Polycarbonate: Excellent optical clarity and impact resistance, widely used in eyewear and safety gear.
- Polypropylene: Versatile and resistant to many chemical solvents, often used in household items and automotive components.
Benefits of Injected Molded Plastic
The adoption of injected molded plastic brings a multitude of advantages that make it a favorite among manufacturers. Here are some key benefits:
1. Cost-Effective Production
One of the most substantial advantages of using injected molded plastic is the ability to produce high volumes at a lower cost. With the efficiency of the injection molding process, businesses can achieve significant savings on both materials and labor.
2. Versatility and Design Freedom
Injected molded plastic allows manufacturers to create complex shapes and intricate designs that would be difficult or impossible to achieve with other manufacturing methods. This versatility opens up endless possibilities for product innovation.
3. Strength and Durability
Products made from injected molded plastics exhibit high strength and durability. Due to their resistance to impact, moisture, and chemicals, these products are ideal for various applications, including automotive parts, household goods, and industrial components.
4. Lightweight Nature
Compared to metals and glass, injected molded plastic products are substantially lighter. This attribute is particularly beneficial in industries like aerospace and automotive, where reducing weight can lead to improved fuel efficiency.
Applications Across Various Industries
The versatility of injected molded plastic means it is utilized in an array of industries. Let's take a closer look at some of the sectors benefiting from this innovative technology:
1. Consumer Goods
From packaging to household items, injected molded plastics are everywhere. Popular consumer products such as containers, toys, and electronic casings often utilize this manufacturing process to optimize functionality while reducing costs.
2. Automotive Industry
The automotive industry has embraced injected molded plastic with open arms. Interior and exterior components, from dashboards to bumpers, are manufactured using this method, providing both aesthetic appeal and structural integrity.
3. Medical Applications
In the medical field, injected molded plastics play a crucial role in the production of devices such as syringes, surgical instruments, and housings for diagnostic equipment. High precision and biocompatibility make this process essential for medical manufacturing.
4. Electrical and Electronics
Electrical enclosures, connectors, and components are often produced through injection molding. The insulating properties of plastics ensure safety and efficiency in electrical applications.
How DeepMould.net is Leading the Way
DeepMould.net is at the forefront of the injected molded plastic industry, providing high-quality solutions tailored to specific customer needs. Here’s how they excel:
1. Custom Mold Design
Understanding that each product is unique, DeepMould.net specializes in creating custom molds that meet precise specifications. This capability ensures that clients receive tailored solutions that maximize their products' functionality and market appeal.
2. Advanced Technology Integration
By leveraging the latest advances in manufacturing technology, DeepMould.net ensures efficiency and accuracy in the injection molding process. Their state-of-the-art equipment is designed to handle complex designs without compromising quality.
3. Commitment to Sustainability
DeepMould.net recognizes the importance of environmental stewardship. They strive to incorporate eco-friendly practices in their production processes and materials, utilizing biodegradable plastics whenever possible.
4. Extensive Industry Experience
The leadership at DeepMould.net brings years of industry experience, allowing them to navigate challenges effectively and deliver superior customer service. Their expertise is invaluable in providing insights into market trends and product development.
The Future of Injected Molded Plastic
As we look to the future, the role of injected molded plastic in manufacturing is expected to grow. With advancements in technology such as additive manufacturing and smart materials, the possibilities are endless. Here are a few trends to watch:
1. Automation and Robotics
Incorporating automation in the injection molding process can enhance efficiency, reduce production time, and minimize human error. As industries move towards smart factories, robotics will play a critical role in the advancement of this manufacturing method.
2. Enhanced Material Science
With ongoing research in materials science, we are likely to see the development of new plastics with enhanced properties. This could lead to better performance, increased durability, and more eco-friendly options for consumers.
3. 3D Printing Synergies
The integration of 3D printing with injection molding can create hybrid manufacturing processes that combine the benefits of both technologies, enabling rapid prototyping followed by large-scale production.
Conclusion
In summary, injected molded plastic has fundamentally changed the landscape of manufacturing. Its cost-effectiveness, versatility, and strength make it an ideal choice for a myriad of applications. Companies like DeepMould.net are leading the way by providing innovative solutions tailored to the needs of modern businesses, ensuring that they remain competitive in an ever-evolving market.
As we move into the future, the continued evolution in injected molded plastic technology will undoubtedly open up new opportunities for innovation, sustainability, and growth in various industries. It is crucial for businesses to stay informed and adaptable to leverage these advancements for their maximum benefit.