Understanding Die Casting Supplies: A Comprehensive Guide for Metal Fabricators
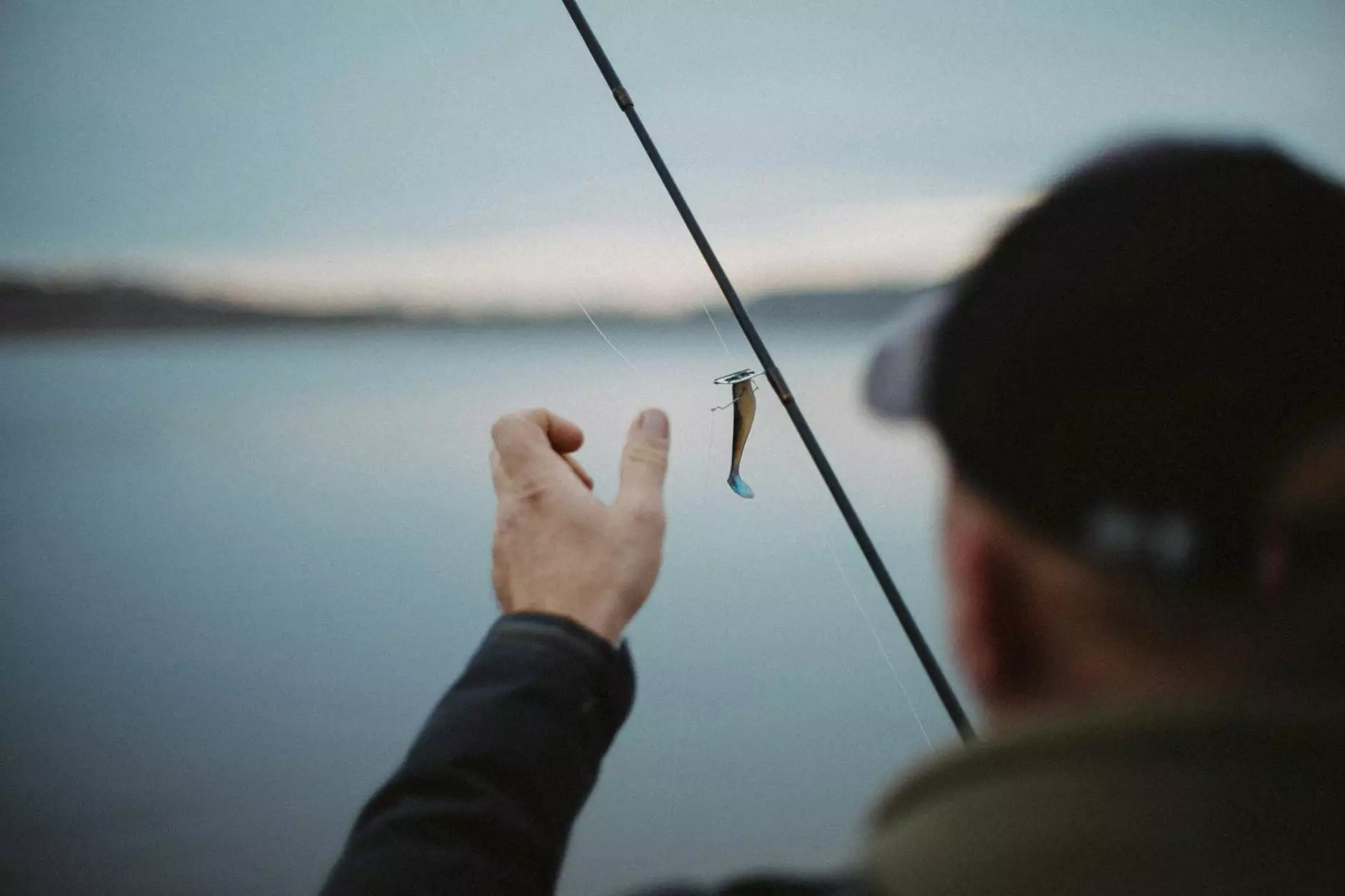
In the world of metal fabrication, efficiency, precision, and quality are paramount. One of the critical processes that facilitate these factors is die casting. This article aims to delve deep into the realm of die casting supplies, exploring what they are, their significance, and their applications in various industries. Whether you are a seasoned professional or a newcomer in the metal fabrication industry, understanding die casting supplies is crucial for enhancing productivity and ensuring quality outcomes.
What is Die Casting?
Die casting is a manufacturing process in which molten metal is injected into a mold cavity under high pressure. The process allows for the production of complex shapes with high dimensional accuracy, smooth surfaces, and excellent mechanical properties. Common materials used in die casting include aluminum, zinc, and magnesium.
Types of Die Casting Processes
- High-Pressure Die Casting: This is the most prevalent method used today and involves injecting molten metal into a mold at high velocity to ensure that it fills every detail of the mold.
- Low-Pressure Die Casting: In this method, molten metal is poured into a chamber, and then the chamber is pressurized to force the metal into the mold, resulting in less stress and more uniform thickness.
- Gravity Die Casting: This traditional method relies on gravity to fill the mold cavity and is typically used for larger castings.
- Permanent Mold Casting: This involves using a reusable mold, allowing for high production runs and excellent surface finishes.
The Importance of Die Casting Supplies
The success of any die casting operation hinges on the quality and reliability of the supplies used. From the molds and machines to the raw materials and protective gear, every element plays a vital role in the die casting process.
Key Components of Die Casting Supplies
Understanding the essential components of die casting supplies helps to grasp their importance in the fabrication process:
- Molds: Molds are crucial for shaping the molten metal. Quality molds are durable, heat resistant, and designed to create precise shapes. Investing in high-quality molds reduces waste and enhances the longevity of the casting process.
- Melting Equipment: Proper melting equipment ensures that the metal reaches the desired temperature for casting. This includes induction furnaces, crucibles, and heating elements that maintain consistent temperatures.
- Injection Machines: These machines inject molten metal into the molds under pressure. Their efficiency, speed, and precision significantly influence the effectiveness of the casting process.
- Raw Materials: The quality of the raw materials used in die casting is vital. Aluminum, zinc, and magnesium alloys are typically used, and their properties significantly affect the final product’s quality.
- Protective Equipment: Safety gear is essential to protect workers from the hazards associated with molten metals and high-pressure equipment.
Benefits of Using Quality Die Casting Supplies
Investing in quality die casting supplies provides numerous advantages for your metal fabrication business.
1. Enhanced Production Efficiency
High-quality die casting supplies streamline the manufacturing process. Efficient machines and molds reduce downtime, leading to an increase in production capacity and lower operational costs.
2. Improved Product Quality
Utilizing superior materials and equipment results in castings with better surface finishes and dimensional accuracy. This improvement reduces the need for secondary machining processes, ultimately saving time and costs.
3. Greater Design Flexibility
With advanced die casting supplies, manufacturers can create complex shapes and designs that are not achievable through other manufacturing processes. This flexibility allows businesses to cater to a broader range of customer needs and industry applications.
4. Enhanced Durability and Strength
Products created through quality die casting exhibit excellent mechanical properties, including strength and durability. This makes them suitable for demanding applications in industries such as automotive, aerospace, and electronics.
5. Environmental Benefits
Modern die casting techniques are more sustainable than ever. By investing in high-quality die casting supplies, companies can minimize waste and enhance resource efficiency, contributing to greener manufacturing practices.
Applications of Die Casting Supplies in Various Industries
The versatility of die casting supplies allows for their applications across numerous industries. Here are some notable examples:
Automotive Industry
In the automotive sector, die casting supplies are used extensively to produce components like engine blocks, transmission cases, and structural parts. The lightweight and durable nature of die-cast parts contributes to overall fuel efficiency and performance.
Aerospace Industry
Die casting plays a critical role in aerospace manufacturing, where precision and reliability are non-negotiable. Components such as brackets, housings, and intricate structural elements are produced using high-quality die casting processes.
Consumer Electronics
In the electronics sector, die casting is utilized to manufacture housings and frames for devices like smartphones, laptops, and gaming consoles. The high aesthetic appeal and durability of die-cast parts enhance the user experience.
Medical Devices
Die casting supplies are crucial in the medical industry, where precision parts are necessary for devices and machinery used in healthcare. Components like casings and connectors must meet strict regulatory standards, and quality casting supplies help achieve this.
Construction Sector
In construction, die casting is employed to produce various fittings, frames, and structural components. Their strength and lightweight properties make them ideal for modern construction techniques.
Choosing the Right Die Casting Supplies Supplier
When it comes to sourcing die casting supplies, selecting the right supplier is critical for your business's success. Here are some factors to consider:
- Quality Assurance: Ensure the supplier provides high-quality products that meet industry standards. Look for certifications and quality control processes.
- Technical Support: A reputable supplier should offer technical support, guidance in selecting appropriate supplies, and assistance in resolving issues that may arise.
- Delivery and Reliability: Timely delivery is essential for maintaining production schedules. Choose suppliers with a proven track record of reliability.
- Cost-Effectiveness: While quality should not be compromised, it's essential to find competitive pricing. Consider the total cost of ownership, including potential savings from reduced waste and downtime.
- Flexibility and Customization: Look for suppliers that offer customization options to cater to your specific needs in terms of materials and design.
Conclusion
In conclusion, the significance of die casting supplies in the metal fabrication industry cannot be overstated. Their impact on production efficiency, product quality, and overall operational success is profound. By understanding the various components and their applications, metal fabricators can make informed decisions that enhance their business operations.
At DeepMould.net, we are committed to providing top-quality die casting supplies tailored to meet the needs of our clients across various industries. By choosing the right suppliers and investing in quality materials and equipment, businesses can achieve remarkable results, driving success in a competitive market. Embrace the power of die casting supplies and watch your fabrication capabilities soar.